Thermography Analysis
At NTIL, we conduct infrared thermal imaging of machinery and electrical panels, helping us to detect faults before they become major issues. Our thermal imaging equipment produces accurate real time high resolution images, enabling engineers to detect problems that might otherwise go unnoticed.
This gives you the opportunity to undertake remedial works prior to costly system failures or production stoppages occurring. Using infrared thermography is effective across all sectors in helping to reduce maintenance costs and even identify possible improvements.
With help of thermography analysis we can analyze the patterns within the surface temperatures to detect a problem before it manifests itself in a costly system failure; thereby saving thousands of rupees. It is an excellent diagnostic maintenance tool that improves both efficiency and reliability of plant systems.
Thermography surveys are conducted while your equipment is working and under is normal operational conditions, any problems will be quickly located allowing you time to schedule maintenance when it is convenient for your business.
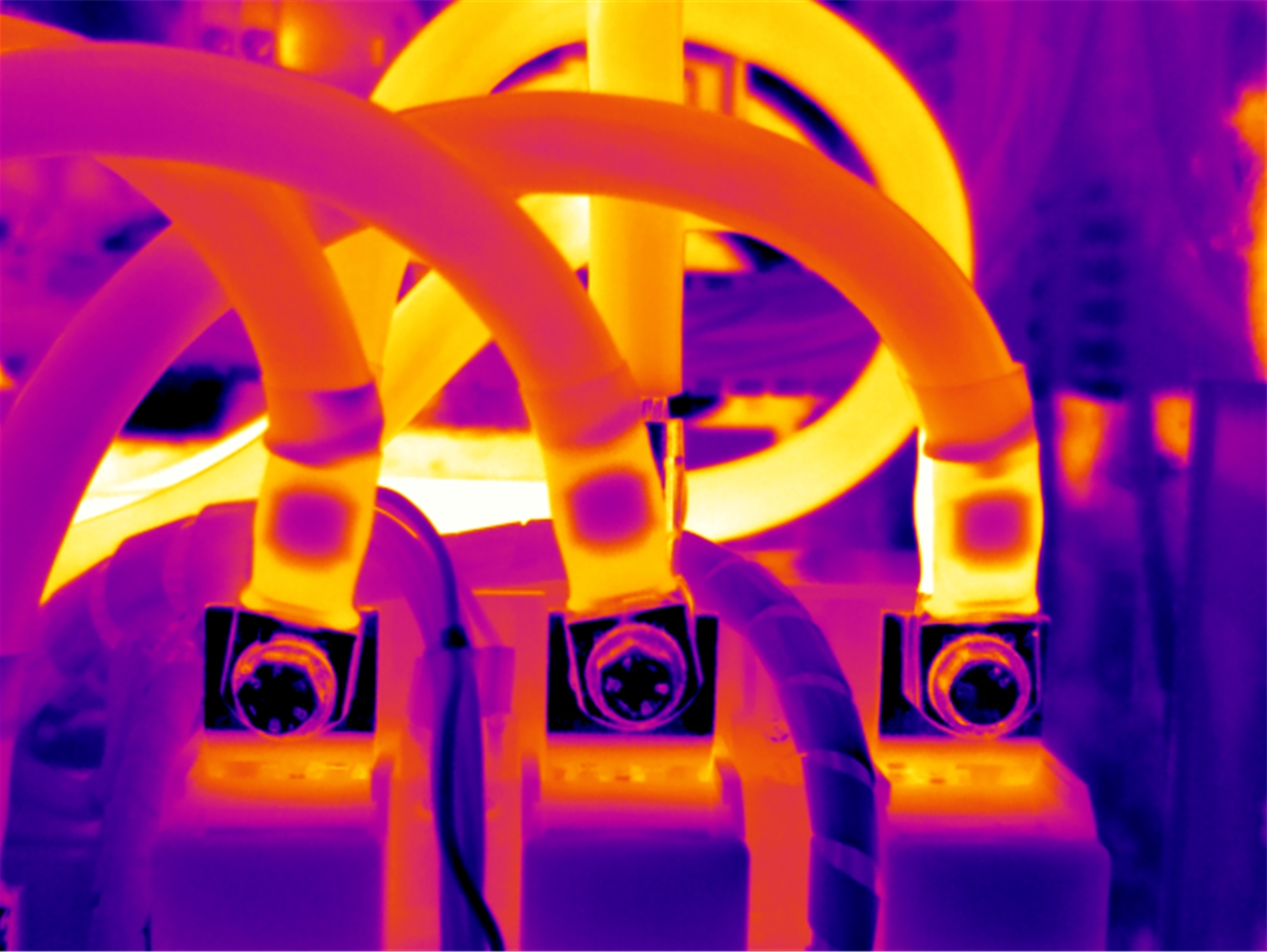
While all properties can benefit from a Thermographic scan, those with high power consumption, multiple branch circuits and distribution subsystems, or heavy equipment have the greatest need. Businesses with high electrical demands should have a thermographic scan performed at least annually on critical systems, such as circuit panels, switchgears, and transformers. Based on the scan results, a schedule to rescan should be based on the types of equipment, power consumption, and age of the electrical systems.
We recommend regular thermography surveys of the following types of equipment:
- Fuse boards
- Distribution boards
- Busbar systems
- Control panels
- High voltage and medium voltage systems
- Power line connections and insulators
- Switchgear
- Electronic components
- UPS and battery systems
- PLC connections
- Motor control centers
- Transformer
- DG Set
- Determines if the components and system have been properly installed and are not damaged
- Reduces downtime
- Reduces risk of equipment failure
- Increases safety
- Determines if components and systems are in compliance with the project specifications and design
- Reduces liability exposure of the designers and installers
- Improves system performance
- Determines whether components and systems operate properly and meet the design intent
- Improves insurability
- Reduces construction schedule delays
Other advantages to detecting and repairing these faults are the cost savings from energy conservation and lower outage and repair costs. High resistance in circuits causes an increase in current flow. When current flow is increased, the resulting power consumption will increase. Further, high current draw can cause critical electrical circuit components, such as fuses, circuit breakers, and transformers, to fail prematurely. These failures result in higher maintenance and repair costs, and resultant business interruptions.